Construction Quality Reviews
A site-based review of the quality of your construction, identifying strengths, weaknesses and root causes.
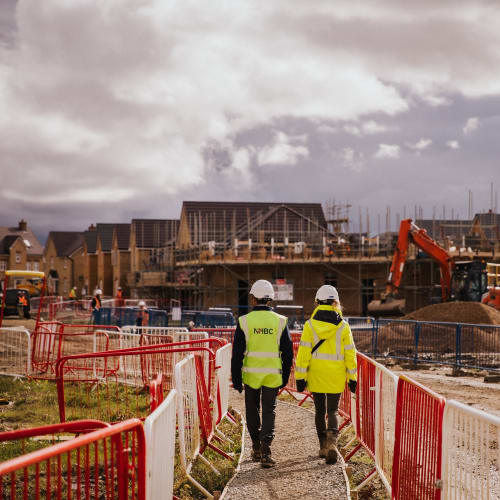
Independent, expert support to improve site quality
A Construction Quality Review (CQR) is an independent, site-based review of the quality of your construction. Conducted by one of our experts, a CQR can be tailored to meet your needs - whether it’s a comprehensive review of up to 38 build stages or a focused assessment of specific areas.
Each review results in a detailed report highlighting strengths, pinpointing weaknesses and uncovering their root causes, all backed by photos and scoring. We don’t just stop at individual sites - our comprehensive analysis compiles all your CQR results to give you a big-picture view of your company’s construction quality. Plus, we’ll benchmark your performance against national and regional standards so you know exactly where you stand.
How does it work?
In advance
We will contact the site representative with a date and time for the CQR, providing at least 24 hours notice.
On the day
There will be an initial meeting with the site representative to gain an overall view of the site and build quality.
Site review
It takes approximately an hour and a half to three and a half hours, depending on the type of CQR, and captures as many build stages as possible. We will thoroughly investigate quality issues and their underlying causes and offer informal guidance and tips to improve build quality. Before leaving the site the reviewer will provide high-level feedback and explore root causes.
Following the review
At a site level, you'll receive a detailed report covering the work seen on the day. Each build stage will include detailed comments, a 6-point scoring scale, photographic evidence and root causes.
Depending on the volume of CQRs you commission, we will provide detailed reporting at a business level to highlight trends and benchmark internal performance between business units and against national and regional peers.
How can it help you?
Enhanced quality
By investing in CQRs, you will demonstrate your commitment to ensuring and maintaining high quality by adopting a right-first-time approach.
Customer satisfaction
Reduce errors and customer complaints and better manage customer expectations and requirements.
Reduced costs
Reduce costs of poor quality through decreased rework, fewer defects and less waste, alongside lower customer service and complaints handling costs.
Types of Construction Quality Reviews
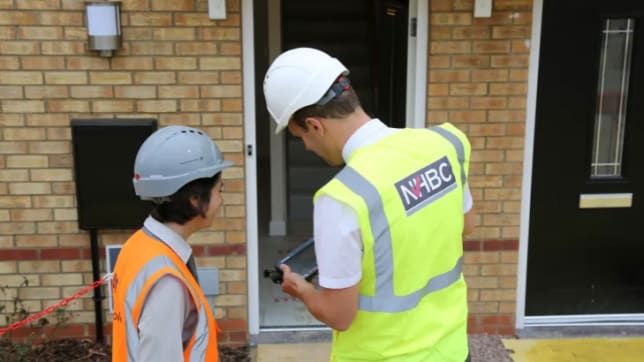
Builder Construction Quality Reviews
Maximise your site’s potential with our Builder Construction Quality Reviews (CQRs) - a comprehensive, independent review covering all key trade areas across your site.
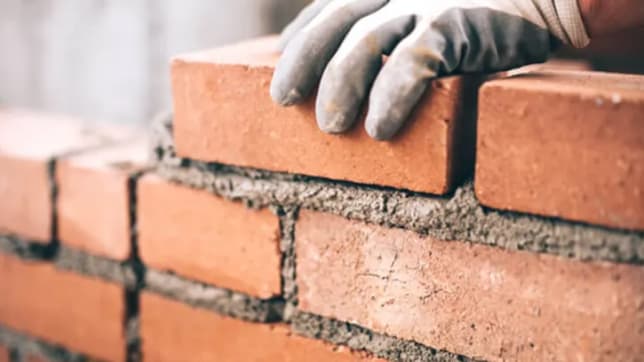
Bricklaying Construction Quality Reviews
Elevate your site’s craftsmanship with our Bricklaying Construction Quality Reviews (CQRs) – a precise, independent evaluation of brickwork quality tailored to your site.
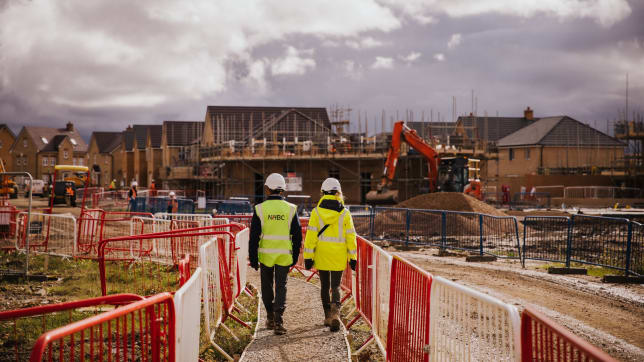
Groundworking Construction Quality Reviews
Unlock unparalleled site performance with our Groundworking CQRs – an expert-led, independent review of groundworking quality across your site.
You may also be interested in...
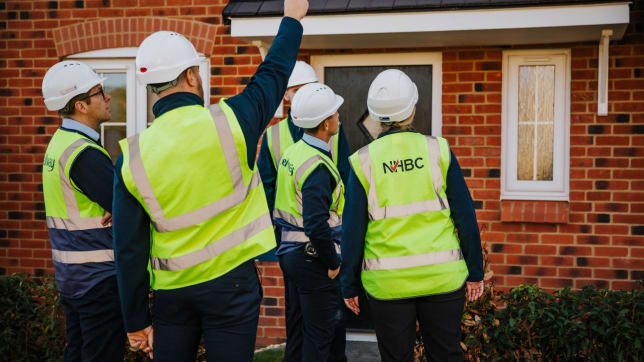
Immersive Days
Fully interactive quality session on your site(s) looking at trending quality issues or specific focus areas of your choice.
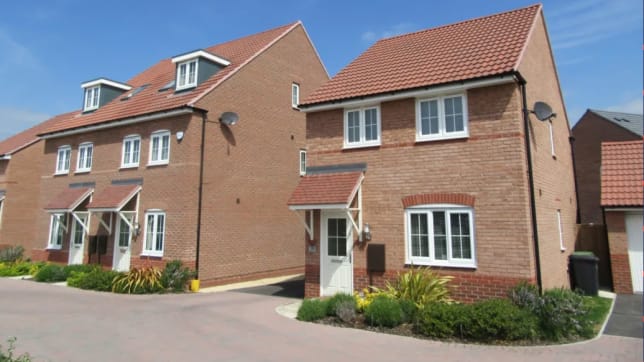
Construction Quality Photo Export
A picture says a 1000 words, especially in high definition. Receive the photos from your Construction Quality Review.
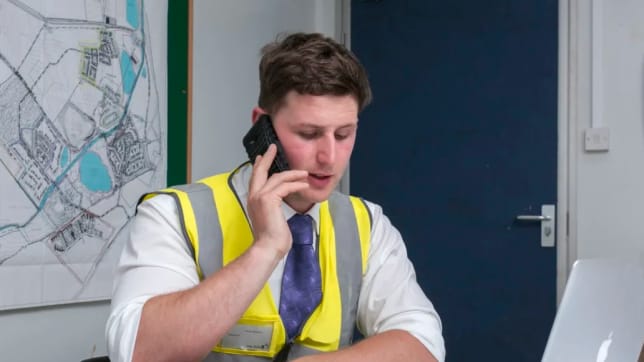
Monthly or Quarterly Quality Related Data
Monthly or quarterly build quality performance updates (based on CQR data) at industry, regional or business level.
Start your construction quality journey now, get in touch
Complete the webform below and we'll get in touch within three working days.
Construction Quality Services
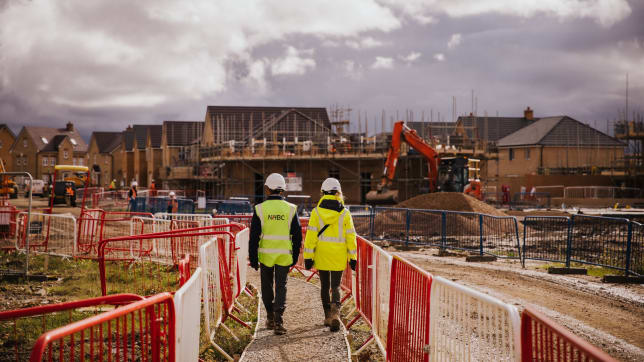
Construction Quality Reviews
A site-based review of the quality of your construction, identifying strengths, weaknesses and root causes.
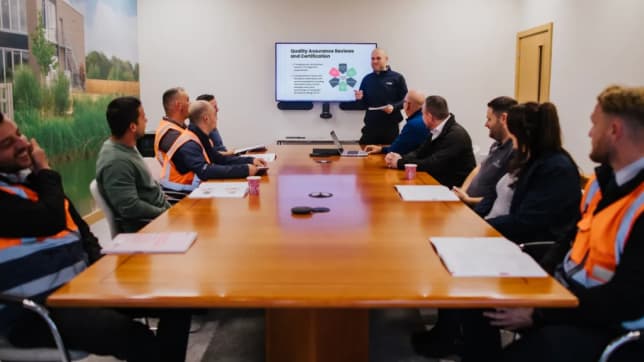
Quality Assurance Reviews and Certification
A business review of quality assurance (processes, procedures, competencies and policies) with potential NHBC QA certification.

Continuous Improvement Programme
A structured methodology to continuously define, measure, analyse, improve and change problematic build areas.
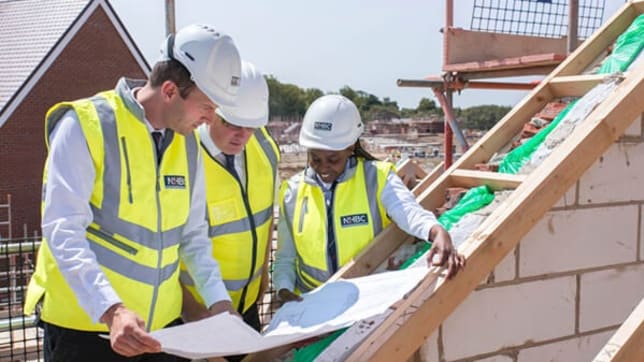
Build Quality Inspections
Additional bespoke inspections for problematic areas or particular build phase for independent review and advice.
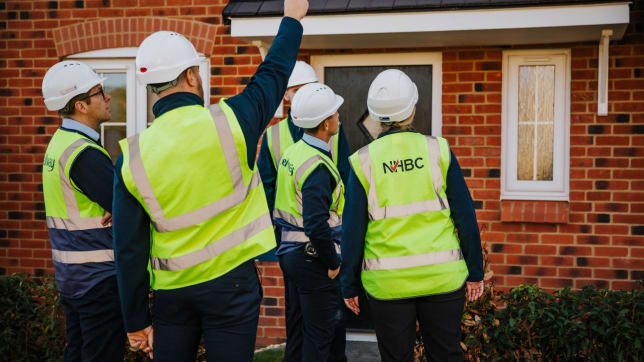
Immersive Days
Fully interactive quality session on your site(s) looking at trending quality issues or specific focus areas of your choice.