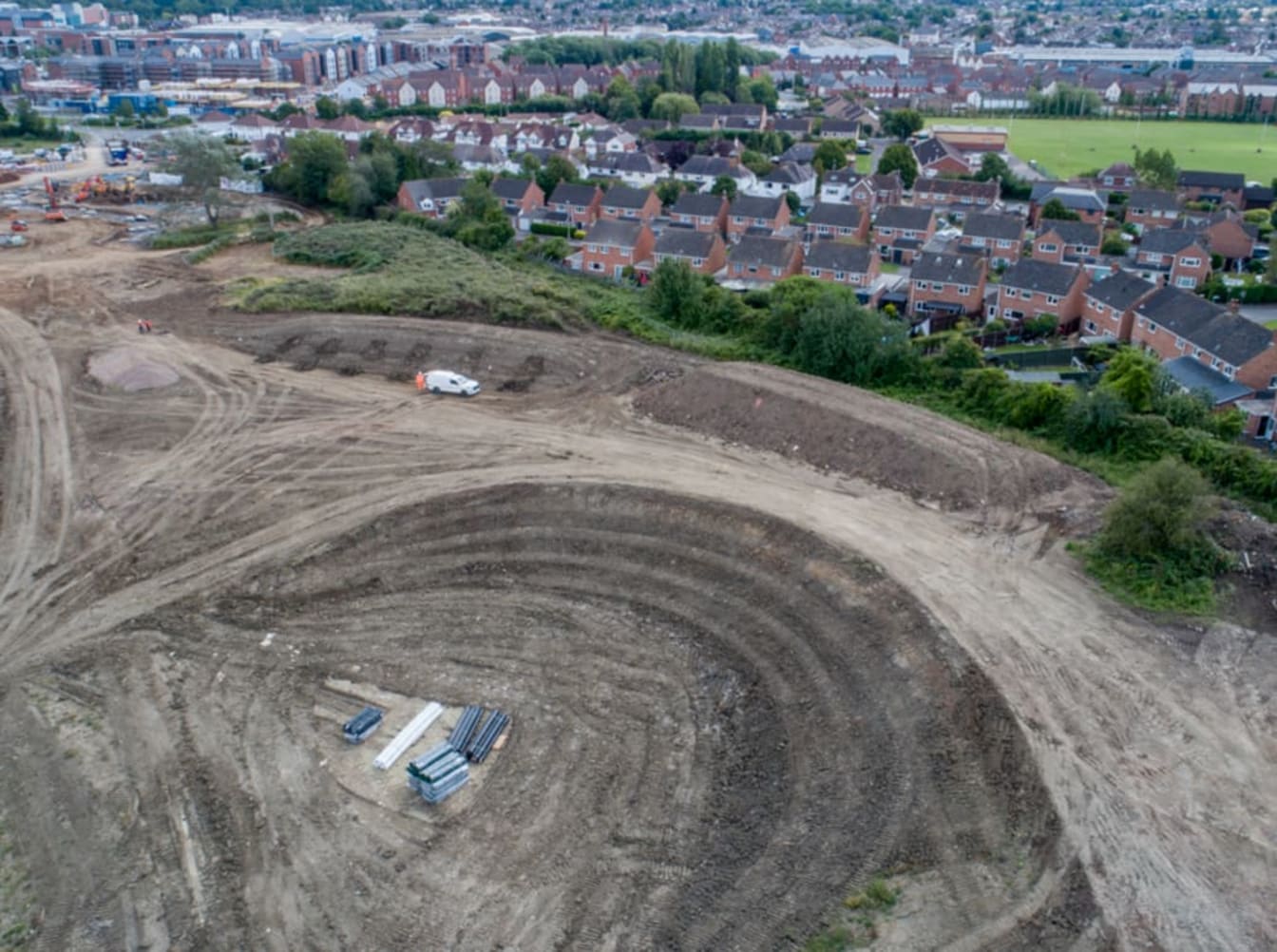
The plan
Lioncourt Homes were looking to reinvigorate this disused brownfield site and create 70 new dwellings across the 6.5 hectares.
The carefully considered layout for the development kept the dwellings to the centre and east, away from the former tank farms where the levels would have required additional uplift to create a geotechnically suitable platform.

The challenge
The main challenge on this site was the legacy of fuels and hydrocarbons, potential per- and polyfluoroalkyl substances (PFAS) contamination and minimising the geotechnical issues due to the differing site levels. There was also an offsite landfill to the north and a major river close by to the west, with the site sloping towards it.
Finding the right solution
To enable a staged build approach the site was tackled in phases with a complete removal of infrastructure before earthworks and remediation were undertaken. LQS supported Lioncourt homes by splitting the site into two phases originally, but this was later revised into an additional two parcels of land due to complications with the weather, the discovery of a badger sett and other technical issues.
At each stage the LQS team were able to assist them with critical geotechnical and geo-environmental advice early in the process and allow works to start on the first 14 plots at the front of the site in 2021. This not only provided reassurance, but also de-risked the site and caused minimal disruption to the planned build phasing.
Ensuring land quality
The project began in 2020 with a Land Quality Evaluation (LQE) report. The LQS team were then commissioned to undertake the Stage 3 element for parcel 2 in 2023 and parcel 3 in 2024. The site was handed over by LQS in full in June 2024.
Steve Barton, Engineering Manager at Lioncourt Homes said “We were excited to be able to progress this development on a brownfield site and knew from the outset that there might be unanticipated elements, not least because of the sites previous use. Working with the LQS team at NHBC helped us ensure we had the right support when we needed it and could adapt our plans in a way that kept the project moving and helped us deal with the unexpected, while still progressing the build programme and maintaining high quality standards.”